OSIRIS -
Saddleback College Robotics Team


Background
The University Rover Challenge (URC) is the world's premier robotics competition for college students. Held annually in the desert of southern Utah in the United States, URC challenges student teams to design and build the next generation of Mars rovers that will one day work alongside astronauts exploring the Red Planet.
Leadership Structure

Proposed Tests, Designs, Calculations
System Design Test for Drivetrain

Wheel Hunting

Decided to go with TPU due to it's ideal properties given our testing scenarios and thereby minimizing chances of brittle failure.

Motor Calculations
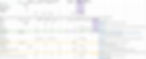
CAD Renders and Designs
Designed and assembled 450-part suspension, employing iterative design principles, GD&T Tolerance Stack-Up, and Root Cause Analysis to ensure all weight and size requirements are fulfilled prior to manufacturing.



The suspension system is a rocker-bogie design with a rear-mounted differential bar, giving the rover optimal stability over rough terrain. Benefits of this design over previous iterations include 20% cheaper and less parts.
Then, I established pre-production testing for 6 custom-designed thermoplastic wheels using SolidWorks’ Finite Element Analysis simulations. Each wheel is successfully able to withstand an applied force of 250 Newtons.


Bill of Materials

Manufacturing



Manufactured and machined various drive components using hand tools, CNC routers, mills, lathes, drill presses, and 3D Printing to reduce outsourcing. Decreased total drivetrain costs by 35%.
The drivetrain consists of six wheels, the forward and backward-most wheels are powered by Rev Robotics NEO brushless DC motors connected to 100:1 gearboxes, capable of 260 Nm of torque. The wheels are printed, airless 250-millimeter TPU tires engineered to absorb bumpiness over rocks, maintain stability, and be simulated to withstand 250 N of applied force.
For motor control, there exist dual-motor controllers capable of up to 120 amps of continuous current.
The drivetrain is powered by three lithium-ion polymer batteries, chosen for their high energy density and discharge capabilities.

Motor Systems
Assembly, Integration and Drivetrain Testing



OSIRIS Rover Test
Full Report
Final Scores
Beat Cornell and UC San Diego as a community college team!
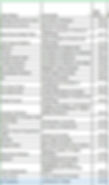